By: Ethan Hofer, Bass, Patrick; Liu, Jiachen; Cai, Yancen; Cheng, Zhongyang
Electroactive polymers (EAPs), also known as artificial muscles, are an exciting new branch of smart materials. Ionic EAPs, a subset of electroactive polymers, contain an electrically insulative polymer matrix as well as ions that can freely move through the polymer. When subjected to a voltage, ions move to different sides of the film depending on their charge, and the size difference of these ions expands one side of the polymer, resulting in an overall bending or curling actuation. These EAPs, with their unique function and low operating voltage, are being studied for potential applications ranging from airplane wings to artificial organs. The goal of this project was to improve EAP actuation and control the ion concentration throughout the polymer for a more dynamic response.
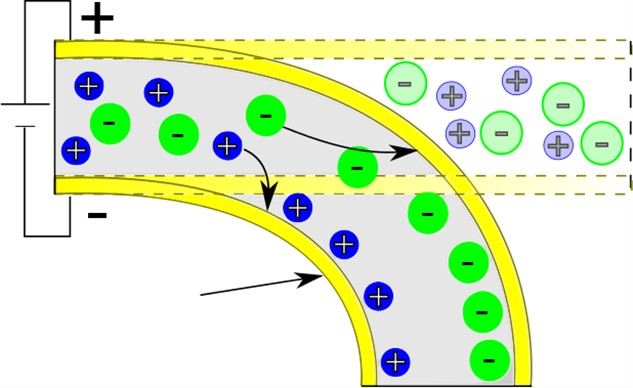
We created EAPs using a solution casting process of polyvinylidene fluoride (PVDF) copolymer doped with cobalt perchlorate. Based on thermal analysis and the optic properties of the polymer films, we found that two different phases often form during the casting process. Tests showed the second phase is detrimental to the actuation response, so we investigated modifications to the casting process to create films with a uniform structure. Methods such as increasing and decreasing the air flow during the casting process as well as dampening the mechanical vibration of the furnace in which the polymers were cast were examined. Additionally, post-casting surface treatments were done to determine their effects upon the performance of the EAPs. Figure 1. Ionic EAP bending mechanism when a surface charge is applied
While the second phase within the thin film was never completely eliminated, notable progress was achieved in decreasing its presence. The surface treatments did not aid in the EAP actuation as they would dissolve the cobalt perchlorate in the polymer, but the dampening of the mechanical vibrations improved the film quality considerably. The evaporation rate during the solution casting is one of the key factors to controlling the microstructure of the films. Because the solution is cast on glass slides, the evaporation rate is difficult to control, as the solvent will evaporate at different rates at different locations on the slides. Because of the two phases, a region’s observed actuation did not accurately represent the concentration of ions in the region. This made it challenging to create an EAP with a designed actuation shape based on the local concentration of ions and the electromagnetic field. Consequently, further research will focus on forming a uniform PVDF thin film. Once this is accomplished, the effect of electromagnetic fields on the ion concentration throughout the film will be studied to create ionic EAPs with a dynamic bending actuation.
Statement of Research Advisor
The EAPs studied by Mr. Hofer exhibit a new type of electromechanical response (i.e., actuation). There are
many factors/issues to be solved/addressed to create engineering devices, or actuators, using the EAPs. In this
project, Mr. Hofer solved one of the factors by designing experiments and identifying possible issues for future
study.
—Zhongyang Cheng, Materials Engineering.
Last Modified: